How is GoldSim Different?
Comparing GoldSim to Traditional Engineering Risk and Reliability Approaches
When discussing how GoldSim differs from other approaches, it is useful to differentiate reliability modeling from risk analysis. The GoldSim Reliability Module can be used for both types of analysis. With conventional methods, however, these two types of analysis use very different types of tools (since they are focused on different types of results).
- Conventional Approaches to Reliability Engineering
- Conventional Approaches to Engineering Risk Analysis
- The GoldSim Approach to Reliability Modeling and Risk Analysis
Conventional Approaches to Reliability Engineering
Most traditional reliability modeling approaches involve the assumption of a static model, where the system configuration never changes (other than due to the failure/repair of components), and where its properties don’t change with time. This is a convenient assumption, as it allows the use of simple techniques, such as closed form mathematical equations or reliability block diagrams. Markov chains are another conventional reliability approach, and although they introduce an element of dynamism, the system itself (and its properties) cannot change with time. Because of the simplifying assumptions required to use these conventional techniques, they may be inappropriate for some systems.
Some of the difficulties with using these approaches for complex systems are summarized below.
- Closed-Form Equations: These methods are heavily dependent on classical models (i.e., they have been primarily developed for use with standard failure distributions like the Poisson and Weibull). Even if failure data can be fitted to a standard distribution, it is difficult to model complex systems with closed form equations. For example, if a system has two Weibull failure modes, they cannot be algebraically combined into a single Weibull failure mode for use with the Weibull reliability equation.
- Reliability Block Diagrams: Reliability block diagram models are static and do not account for the highly dynamic nature of many systems. A reliability block diagram model also assumes the system is in steady state, and unless correction factors are used, assumes that all of its components are independent.
- Markov Chains: Markov chains enumerate a number of system “states” and the probabilities for transitioning between these states. However, the number of transition probabilities (and the computational effort) required to solve a Markov chain grows exponentially with the number of states. Because of this “state-space explosion”, in many cases a system must be greatly simplified in order to use a Markov chain approach.
Of course, the conventional approaches are appropriate for many systems, particularly when employed by an experienced practitioner. However, in some cases, a more realistic reliability model may be required.
Conventional Approaches to Engineering Risk Analysis
Risk analysis is a very broad field, utilizing a variety of quantitative approaches. In the current context, however, we are primarily concerned with risk analysis of complex engineered systems (e.g, nuclear power plants, infrastructure such as dams, and space and defense systems) that are composed of highly-reliable and frequently redundant components, which in most cases are required to have an extremely low risk of a catastrophic failure.
The conventional approach to risk analysis for such systems focuses on the analysis of initiating events and subsequent event sequences that could lead to failures, and on enumerating and calculating the probabilities of different outcomes through tree-based analytical procedures (event trees/fault trees).
For many types of systems (e.g., nuclear power plant probabilistic risk assessments), these approaches work well. However, systems that are highly dynamic or have significant process variability can be very difficult to model realistically using event tree/fault tree approaches, and they require a tremendous amout of preprocessing effort.
As a result, an approach like GoldSim's that facilitates explicit representation of dynamics and variability potentially provides a powerful complement to existing methods.
The GoldSim Approach to Reliability Modeling and Risk Analysis
GoldSim is a general purpose dynamic, probabilistic (Monte Carlo) simulator. Dynamic simulation allows the analyst to develop a representation of the system whose reliability is to be determined, and then observe that system’s performance over a specified period of time.
The primary advantages of dynamic probabilistic simulation are:
- The system can evolve into any feasible state and its properties can change suddenly or gradually as the simulation progresses.
- The system can be affected by random processes, which may be either internal (e.g., failure modes) or external.
- If some system properties are uncertain, the significance of those uncertainties can be determined.
In Monte Carlo simulation, the model is run many times with uncertain variables sampling different values each time (each run is called a realization). Each realization is considered equally likely, and their results can be combined to provide not only a mean, but also confidence bounds and a range on the performance of the system. In addition to the statistical data these realizations provide, multiple realizations may also reveal failure modes and scenarios that may not be apparent, even to experienced risk and reliability modelers.
With GoldSim, you can:
- Model components that have multiple failure modes: GoldSim allows you to create multiple failure modes for components, each of which can either be defined by a distribution or occur when a specified condition arises. Failures which occur according to a distribution do not have to use time as the control variable. For example, a vehicle might use mileage to define failure, while an aircraft might use the number of cycles.
- Model complex interdependencies: In addition to providing a logic-tree mechanism to define relationships, GoldSim also allows you to model the more subtle effects of failure on other portions of the system. For example, you can easily model a situation where the failure of one component causes another component to wear more quickly.
- Model the external environment: Reliability elements in GoldSim are fully compatible with all other GoldSim elements. This means that the environment in which the system operates can also be modeled, and can affect and interact with the system.
These features and capabilities provide a powerful engine for realistically modeling the risk and reliability of complex engineered systems.
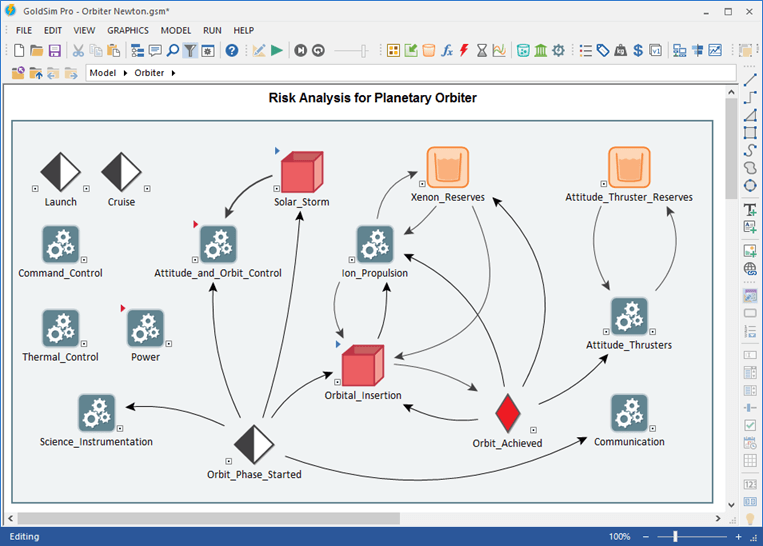
Learn More
To learn more, download this White Paper, which compares and contrasts GoldSim to traditional approaches in much greater detail: